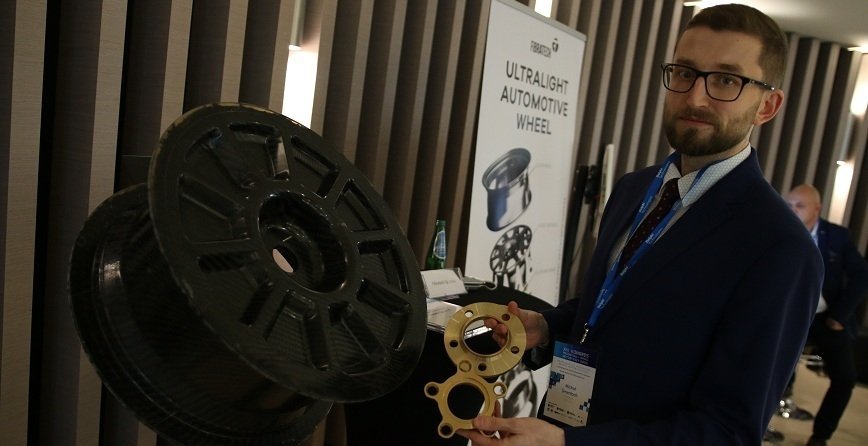
Michał Smentoch, dyrektor zarządzający firmy Fibratech. fot. Piotr Łukaszewicz
Felgi polskiej spółki Fibratech przeszły pozytywnie testy bezpieczeństwa TUV. Oznacza to, że ultralekkie obręcze mogą wkrótce trafić do masowej produkcji. Felgi wykonane z kompozytu węglowego będą lżejsze i sztywniejsze od standardowych aluminiowych, dostępnych na rynku.
Według danych opublikowanych przez BusinessWire rynek felg kompozytowych ma ogromny potencjał wzrostu. Można mówić nawet o rewolucji.
Dla założycieli spółki - Michała Smentocha, dra inż. Michała Sobolewskiego i dra inż. Bayreuthera - technologia ma być przede wszystkim bezpieczna dla użytkowników. - Dlaczego testy TUV są tak istotne? Potwierdzają one gotowość technologiczną produktu. W trakcie testów odzwierciedlane są obciążenia występujące podczas użytkowania pojazdu z zachowaniem rygorystycznych współczynników bezpieczeństwa - mówi Michał Smentoch, CEO Fibratech.
W 2017 roku w projekt zainwestował fundusz Alfabeat. Środki zostały przeznaczone na prace badawczo-rozwojowe, które doprowadziły do stworzenia prototypu. Produkt został doceniony m.in w ostatniej edycji konkursu “Orzeł innowacji - Startup”, gdzie zwyciężył w kategorii “Przełomowa technologia”.
Kilka tygodni temu Michał Smentoch udzielił nam wywiadu i szczegółowo opowiedział o technologii.
Konkurencja i technologia
Jak wynika z analiz zespołu Fibratech, firmy proponujące podobne rozwiązania - próbując zastąpić aluminium standardowymi tkaninami kompozytowymi - nie osiągają oczekiwanych rezultatów. Przez konieczność zastosowania wielu warstw materiału, felgi nie stają się lżejsze, a potrzeba sporego zaangażowania ludzi na etapie produkcji przekłada się na wysoką cenę konkurencyjnych rozwiązań.
Twórcy Fibratech opracowali autorską strukturę tekstyliów kompozytowych. Rozwiązanie zakłada ułożenie włókien węglowych w taki sposób, by odpowiadały rozkładowi sił oddziałujących na felgę w trakcie jazdy. Pozwala to na lokalne i kontrolowane wzmacnianie struktury obręczy. To z kolei przekłada się na obniżenie masy felgi, która na etapie masowej produkcji ma ważyć około 8.5 kg (dla rozmiaru 20’’ x 10’’) - czyli 15% mniej niż najlżejsze istniejące na świecie felgi (aluminiowe kute). Co więcej, dzięki takiej redukcji, samochód będzie mógł pokonać dłuższą trasę na tej samej ilości paliwa, co jest szczególnie istotne dla branży elektromobilnej. To ona ze szczególną uwagą przygląda się poczynaniom spółki.
Komentarze (0)