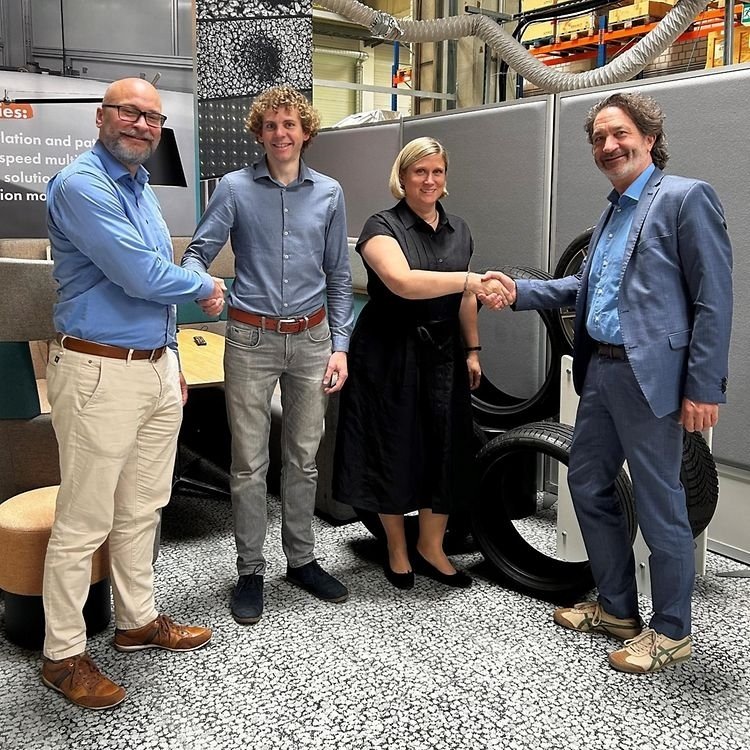
Brak hałasu silnika w pojazdach elektrycznych sprawia, że hałas toczących się opon jest bardziej słyszalny w kabinie. Ale i to się może zmienić odkąd Henkel i 4JET współpracują, aby wprowadzić przełomowy proces produkcji cichych opon przeznaczonych do pojazdów elektrycznych.
W pojazdach elektrycznych (EV) w zależności od nawierzchni drogi i prędkości hałas toczących się opon może być postrzegany jako znacznie bardziej uciążliwy i nieprzyjemny w porównaniu z pojazdami spalinowymi. To dlatego nowoczesne pojazdy elektryczne są często wyposażone w opony z wyściółką z pianki poliuretanowej (PU). Tzw. „ciche opony” znacznie redukują emisję hałasu zarówno wewnątrz pojazdu, jak i w otaczającym środowisku.
Ta z pozoru prosta koncepcja stawia producentów opon na całym świecie przed złożonym i wymagającym zadaniem: wszak cała linia logistyczna musi zostać zintegrowana na nowo, aby transportować lekką, ale dużą objętość pianki, która jest potrzebna na końcu linii produkcyjnej. Wymaga to znacznej przestrzeni do obsługi logistycznej i wielu etapów pośredniego przechowywania pianki. Liczne dodatkowe czynności manualne lub półautomatyczne są wymagane także na czas cięcia, dodawania klejów i wkładania pianki do opony. I wreszcie, dla każdej wyprodukowanej tak opony, odpowiednia pianka musi być dostarczona „just-in-sequence”, tj. w ściśle określonej sekwencji produkcyjnej. W rezultacie koszty produkcji opony wzrastają nawet o 25%, a i tak często okazuje się niemożliwe zintegrowanie technologii z istniejącymi zakładami produkującymi opony. Kolejny problem to powstające odpady z kawałków pianki poliuretanowej.
I tu dochodzimy do innowacyjnego rozwiązania, które jest dziełem Henkel i 4JET.
Loctite LASER-FIT
Henkel i 4JET proponują od niedawna nowy proces produkcji cichych opon, który rozwiązuje powyższe wyzwania. W innowacyjnym procesie LASER-FIT, pianka akustyczna „szyta na miarę” jest produkowana… bezpośrednio wewnątrz opony – a to za sprawą płynnych materiałów wyjściowych, które są aplikowane na końcu linii produkcyjnej opon. Ta metoda eliminuje złożoność procesów, czasochłonną logistykę, a jednocześnie daje producentowi opon większą swobodę w dostosowywaniu geometrii i objętości pianki do rodzaju opony, a tym samym zmniejsza wytwarzanie odpadów.
Przewaga LASER-FIT tkwi w bezpośrednim procesie spieniania, który od dawna jest stosowany w innych branżach dzięki opatentowanemu procesowi aktywacji pianki przy użyciu lasera. Podobnie jak ciasto drożdżowe, pianka tworzy na powierzchni nieprzepuszczalną dla powietrza powłokę. Ta powłoka minimalizuje przenikanie dźwięku do pianki akustycznej o otwartych porach i skuteczniej pochłaniania decybele.
Komentarze (2)