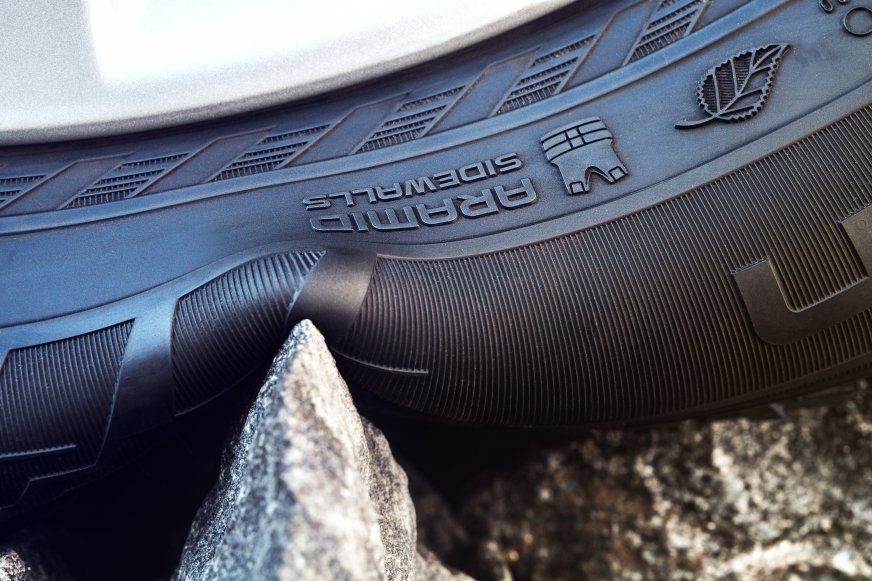
- Oprócz odświeżonego wzoru bieżnika w strukturze, komponentach lub surowcach nowej opony mogło być ponad sto zmian w porównaniu z poprzednim modelem. Zanim opona trafi do sprzedaży, powstają setki różnych prototypów, aby znaleźć najlepszą możliwą kombinację - mówi Matti Morri.
Materiały pochodzenia biologicznego
Te zyskują na popularności. Nokian Tyres nieustannie poszukuje nowych innowacji w dziedzinie materiałów, ale pewne podstawowe elementy są częścią opon już od dziesięcioleci. Przykładami są kauczuk naturalny i sadza, a pojedyncza opona może zawierać kilka różnych ich rodzajów.
- Zbadaliśmy niezliczoną ilość różnych opcji, ale jak dotąd mieszanki gumowe zapewniają najlepsze parametry bezpieczeństwa dla opon. Czarny kolor opony również pozostanie. Oprócz doskonałych osiągów, czarny kolor podstawowy nie uwydatnia brudu, a także utrzymuje zrównoważony i ładny wygląd opony przez cały okres eksploatacji. Testowano opony w innych kolorach, ale były one eksperymentalne, na przykład ze względu na skomplikowany proces produkcji i wysokie koszty. Oczywiście możliwe są indywidualne opony w wybranych kolorach i z wzorami ścian bocznych - wyjaśnia Matti Morri.
Włókno aramidowe używane przez Nokian Tyres jest jednak znacznie rzadszym materiałem. Wzmacnia ono mechaniczną trwałość bieżnika i ściany bocznej opony, na przykład w oponach do samochodów typu SUV i van.
- Fakt, że aramid częściej niż w oponach wykorzystywany jest na przykład w przemyśle lotniczym, mówi wiele o jego wytrzymałości - wyjaśnia Matti Morri.
W przyszłości najważniejsze postępy będą dotyczyły komponentów pochodzenia biologicznego i związanej z oponami technologii czujników i przetwarzania danych. Naszym celem jest, aby do roku 2030 połowa surowców używanych w naszych produktach pochodziła z recyklingu lub była odnawialna. Na przykład jedna trzecia materiałów używanych w mieszance Green Trace w oponach zimowych Hakkapeliitta R5 już teraz pochodzi z takich źródeł. Związek ten wykorzystuje między innymi olej rzepakowy i żywicę sosnową.
Opony produkowane pod jednym dachem
Chociaż jest kilka komponentów, a ich proporcje są ustalane dokładnie co do grama, nie ma różnic w jakości między oponami. Komponenty przenoszone są w sposób kontrolowany i przetestowany do maszyny montażowej, gdzie automatyzacja zajmuje się resztą. Cały proces, od produkcji i odmierzania komponentów po montaż i utwardzanie opony, odbywa się pod jednym dachem – tylko kolce lub pianka dźwiękochłonna używana do poprawy komfortu w oponach EV dodawane są gdzie indziej.
- W przemyśle samochodowym różne komponenty zazwyczaj pochodzą od różnych podwykonawców i są łączone w fabryce samochodów. My robimy to wszystko pod jednym dachem, co zapewnia doskonałą jakość - podsumowuje Matti Morri.
- Naszym celem jest, aby do roku 2030 połowa surowców używanych w naszych produktach pochodziła z recyklingu lub była odnawialna.
Fot. Nokian Tyres
Komentarze (0)